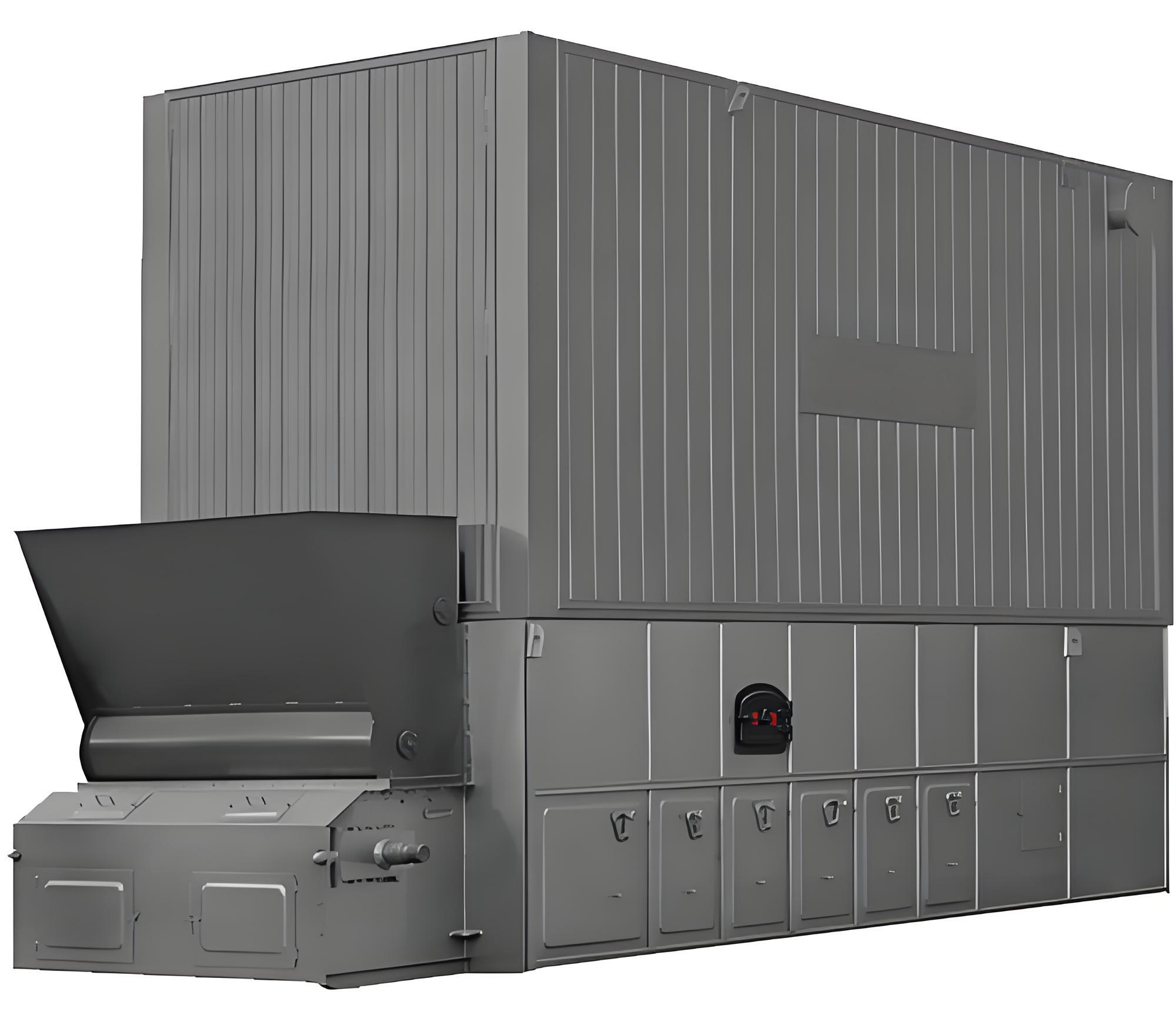
I. Product range:
1. Product model: YLW horizontal coal-fired organic heat carrier boiler
2, rated thermal power: 1.9MW - 35MW(1.6 million kcal - 30 million kcal)
3. Working pressure: 0.6-1.1MPa
4, other: according to the user's various parameter requirements specially designed and manufactured, to provide products to meet customer needs, tailored.
Ⅱ, structural characteristics:
1. YLW furnace series organic heat carrier furnace is a square box assembled forced circulation chain grate boiler. The boiler is composed of the upper body (or the upper body + the lower body) and the lower grate, and the construction site is combined.
2. The radiant heating surface of the boiler body adopts a serpentine convection heat exchange tube at the back of the close-packed square coil in a single furnace or a double furnace.
The tail is equipped with air preheater, steam waste heat boiler and hot water energy-saving device to recover waste heat according to the user's waste heat use, reduce the smoke exhaust temperature, improve the boiler heat efficiency and reduce fuel consumption.
3. According to the fuel characteristics, the convection heat exchange section of the boiler adopts the measures of high and low wrong row, widening the distance and arranging the soot blowing device and ash cleaning device to reduce the boiler ash accumulation and improve the boiler efficiency.
4, boiler heat exchange surface tube adopts automatic argon arc welding, automatic real-time Xlif line online 100% detection, welding quality is stable and reliable.
5, grate using high temperature resistant materials, reasonable arrangement of air cooling form, grate reliable use, long service life
6, the large boiler adopts partial integration, on-site assembly, high integration, convenient and quick on-site installation, saving installation time.
Ⅲ performance advantages:
1. High efficiency and energy saving
(1) The radiation heat exchange section adopts a double-close row coil structure, the convective heat exchange section S-type multi-return heat exchange, and the air preheater is set at the tail.
(2) The tail is configured with air preheater, steam waste heat boiler and hot water energy-saving device for waste heat recovery according to the use of the user's waste heat, reduce the exhaust temperature, improve the boiler thermal efficiency and reduce fuel consumption.
(3) The grate arch is specially designed, the air chamber independently regulates the air setting, the coal combustion is uniform and sufficient, and the medium adaptability is wide.
(4) The boiler uses high-quality insulation materials and special construction technology, less heat loss, low smoke exhaust temperature, and high thermal efficiency of the boiler.
(5) Combining industrial automation control technology, Internet technology, computer software and artificial intelligence technology to establish an industrial boiler Internet of Things platform, which can realize remote human-computer interaction and data sharing, and realize dynamic control.
2, safe and reliable
(1) The body heating surface adopts close-row coil, and the heating surface is adequately arranged to effectively reduce the heat load on the surface of the pipe, and the use of thermal oil medium is safer.
(2) The medium process is reasonable, the heat transfer oil is from the front (import) to the back (export), and the medium gas generated during operation is difficult to stay in the furnace, which can be convenient to discharge the system.
(3) The furnace radiant heat exchange surface adopts double close-row coils, the heating surface is fully arranged, the boiler starts fast at temperature rise, and the load margin is large.
(4) Boiler operation adopts remote and near-ground multi-point control, automatic control and monitoring instruments.
(5) The tail convective heat transfer section adopts a special anti-ash structure design and is equipped with a soot blowing device, which has no ash accumulation and high heat transfer efficiency.
3, Environmental protection according to the local plutonium protection requirements to configure appropriate flue gas treatment equipment, flue gas emissions to meet the environmental requirements.
Coal-fired organic heat carrier boiler(160×104Kcal/h-3000×104Kcal/h)
1、Fan according to the user selected flue gas treatment equipment to do the final parameter verification (increase the flue gas resistance after adding environmental protection equipment)
2, more than 15 million kcal boiler supporting high tank, low tank according to the actual system oil storage capacity design.
3, more than 15 million kcal boiler supporting drum, induced draft fan according to the actual increase in flue gas treatment equipment selection, effectiveness.
4, more than 15 million kcal boiler supporting speed box selection according to the actual working conditions.