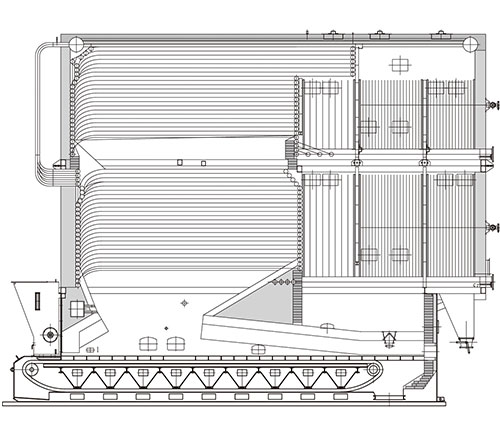
Ⅰ, biomass molding fuel boiler
A boiler that burns biomass molding fuel to heat working medium.
Biomass molding fuel is the use of woody, herbaceous plants (such as straw, rice bran, wood chips, bark, peanut shell, hemp stalk, etc.) and their waste materials as raw materials, with mechanical methods (such as cutting, crushing), dense molding technology, processing into a shape and size, bulk density, conducive to transportation and combustion of molding fuel. It can replace coal, oil and natural gas, achieve energy saving and emission reduction, and greatly reduce production costs compared with oil or gas boilers.
Biomass fuel is a renewable clean fuel, the development of biomass energy instead of oil, coal and other traditional energy, reduce fossil fuel consumption, reduce CO², not only can protect the environment, but also promote the sustainable development of agriculture and forestry, with good ecological and social benefits.
Ⅱ, biomass fuel composition
(1) Agricultural biomass molding fuel
Corn stalk, wheat stalk, straw, bean stalk, sorghum stalk, cotton stalk and other crop straw produced in the process of agricultural production
(2) Agricultural product processing industry leftovers
Residues such as rice husks, corn cobs, peanut husks and other residues produced in the processing of agricultural products are agricultural mixtures and mixtures of various agricultural biomass
(3) Forest biomass fuel
Felling, timber building residues, wood processing residues, tree pruning and forestry mixtures
(4) Mixed biomass fuel
A mixture of agricultural and forestry biomass
Ⅲ, Characteristics of biomass fuel
1. Biomass molding fuel, with easy ignition, good fuel performance, high calorific value, no pollution, after combustion can meet GB13271 "boiler air pollutant emission standard" requirements.
2. Biomass molding fuel, with a significant ratio (1000-1270kg /m3), high calorific value (3800~4500Kcal/kg), volatile content ≥65.6%, combustion rate of more than 90%. Low cost, easy to use, clean and sanitary advantages, easy to store and transport.
3. Biomass molding fuel, a renewable and clean fuel, is a typical circular economy project.
4. Low-carbon energy CO2 zero emissions, biomass fuel is mainly volatile, its fixed carbon content is only 15% on the right, is a typical low-carbon fuel. The CO2 emitted by combustion is absorbed by plants for photosynthesis during the growth process to achieve zero CO2 emission.
5.Low nitrogen and sulfur content reduces sulfur dioxide (SO2) and NOx oxide emissions. The sulfur content of biomass is only 0.06%, which is lower than the sulfur content of light diesel, and it can be directly discharged without the need to set up a desulfurization device.
Ⅳ. Product range:
1, Product model: YLW horizontal burning biomass organic heat carrier boiler
2, rated thermal power: 1.9MW - 35MW(1.6 million kcal - 30 million kcal)
3. Working pressure: 0.6-1.1MPa
4, other: according to the user's various parameter requirements specially designed and manufactured, to provide products to meet customer needs, tailored.
Ⅴ, structural characteristics:
1. YLW furnace series organic heat carrier furnace is a square box assembled forced circulation chain grate boiler. The boiler is composed of the upper body (or the upper body + the lower body) and the lower grate, and the construction site is combined.
2. The radiant heating surface of the boiler body adopts a serpentine convection heat exchange tube at the back of the close-packed square coil in a single furnace or a double furnace.
The tail is equipped with air preheater, steam waste heat boiler and hot water energy-saving device to recover waste heat according to the user's waste heat use, reduce the smoke exhaust temperature, improve the boiler heat efficiency and reduce fuel consumption.
3. According to the fuel characteristics, the convection heat exchange section of the boiler adopts the measures of high and low wrong row, widening the distance and arranging the soot blowing device and ash cleaning device to reduce the boiler ash accumulation and improve the boiler efficiency.
4. Compared with traditional coal-fired boilers, it has a larger furnace combustion space to adapt to the characteristics of high volatile content of biomass fuel.
5, the grate combustion chamber is raised, and the secondary air is arranged: the grate is divided into the air, the air volume is adjusted independently, and the grate is stepless speed regulation.
6, the feeding device has independent intellectual property rights, the use of locking mechanism.
7, grate using high temperature resistant materials, reasonable arrangement of air cooling form, grate reliable use, long service life
8, boiler heat exchange surface tube adopts automatic argon arc welding, automatic real-time Xlif line online 100% detection, welding quality is stable and reliable.
9, furnace radiation heat exchange surface, convection heat exchange surface with special anti-wear structure.
10, the large boiler adopts partial integration, on-site assembly, high integration, convenient and quick on-site installation, saving installation time.
Ⅵ, performance advantages:
1. High efficiency and energy saving
(1) The radiation heat exchange section adopts a double-close row coil structure, the convective heat exchange section S-type multi-return heat exchange, and the air preheater is set at the tail.
(2) The tail is configured with air preheater, steam waste heat boiler and hot water energy-saving device for waste heat recovery according to the use of the user's waste heat, reduce the exhaust temperature, improve the boiler thermal efficiency and reduce fuel consumption.
(3) The grate combustion chamber is raised, the secondary air is arranged to support the combustion, the fuel combustion is uniform and full, and the combustion efficiency is high.
(4) Grate arch special design, grate into the air, independent adjustment of air volume, fuel adaptability.
(5) The boiler uses high-quality insulation materials and special construction technology, less heat loss, low smoke exhaust temperature, and high thermal efficiency of the boiler.
(6) Combining industrial automation control technology, Internet technology, computer software and artificial intelligence technology to establish an industrial boiler Internet of Things platform, which can realize remote human-computer interaction and data sharing, and realize dynamic control.
2, safe and reliable
(1) The body heating surface adopts close-row coil, and the heating surface is adequately arranged to effectively reduce the heat load on the surface of the pipe, and the use of thermal oil medium is safer.
(2) The medium process is reasonable, the heat transfer oil is from low (import) to high (export), the medium gas generated during operation is difficult to stay in the furnace, and it can be convenient to discharge the system.
(3) The furnace radiant heat exchange surface adopts double close-row coils, the heating surface is fully arranged, the boiler starts fast at temperature rise, and the load margin is large.
(4) Boiler operation adopts remote and near-ground multi-point control, automatic control and monitoring instruments.
(5) The feeding device adopts the locking mechanism and distributes the material with secondary air to effectively prevent the flame tempering from burning out the hopper.
(6) The tail convective heat transfer section adopts a special anti-ash structure design and is equipped with a soot blowing device, which has no ash accumulation and high heat transfer efficiency.
3, Environmental protection according to the local plutonium protection requirements to configure appropriate flue gas treatment equipment, flue gas emissions to meet the environmental requirements.
Biomass-fired organic heat carrier boiler(160×104Kcal/h-3000×104Kcal/h)
1、Fan according to the user selected flue gas treatment equipment to do the final parameter verification (increase the flue gas resistance after adding environmental protection equipment)
2, more than 15 million kcal boiler supporting high tank, low tank according to the actual system oil storage capacity design.
3, more than 15 million kcal boiler supporting drum, induced draft fan according to the actual increase in flue gas treatment equipment selection, effectiveness.
4, more than 15 million kcal boiler supporting speed box selection according to the actual working conditions.
5, the above boiler is designed according to biomass molding particles, such as the use of other biomass fuels such as: wood chips, palm shells, bamboo powder and bamboo chips, etc., need to provide a composition analysis report.